Understanding Instrumentation Tube Fittings: A Comprehensive Overview
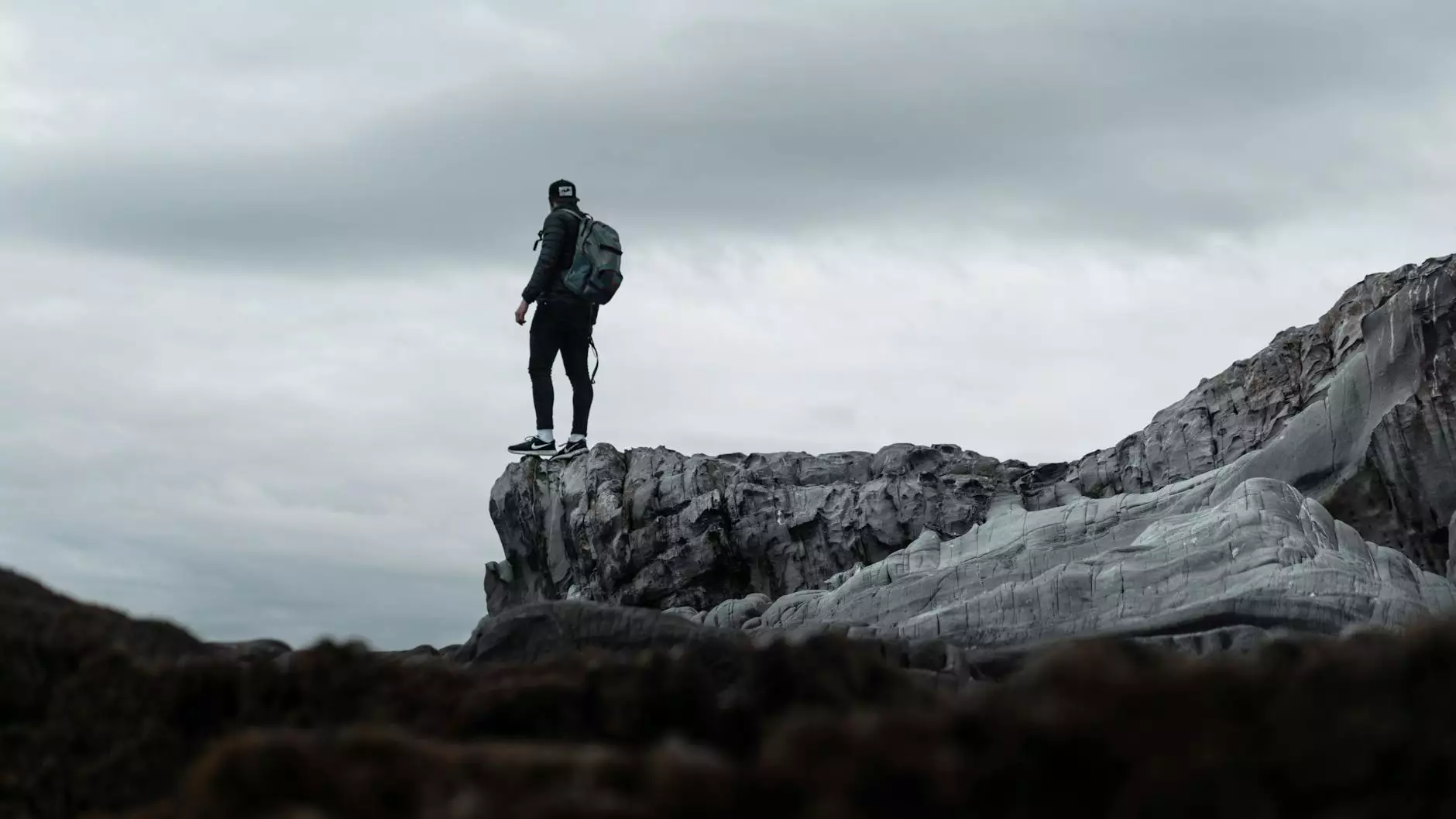
In the realm of modern engineering, instrumentation tube fittings manufacturers play a crucial role in ensuring the smooth operation of various industrial processes. These fittings are essential for connecting tubes in various systems, providing reliability and safety in fluid transfer applications. In this article, we will explore the importance of instrumentation tube fittings, the diverse categories, and the benefits they offer across multiple sectors.
The Importance of Instrumentation Tube Fittings
Instrumentation tube fittings are designed to connect pipes, tubes, and hoses in various industrial applications. They ensure that systems operate correctly and safely by preventing leaks and maintaining the flow of gases and liquids. The manufacturing of these fittings requires precision engineering to meet stringent industry standards.
Key Benefits of Using Instrumentation Tube Fittings
- Leak Prevention: High-quality fittings minimize the risk of leaks, which can lead to hazardous situations.
- Durability: Made from robust materials, these fittings are designed to withstand extreme temperatures and pressures.
- Ease of Installation: Most fittings are designed for quick and easy installation, reducing downtime during maintenance.
- Versatility: Suitable for a wide range of applications, from oil and gas to pharmaceuticals.
Categories of Instrumentation Fittings
Instrumentation tube fittings are categorized into various types, each serving specific functions. Understanding these categories helps businesses choose the right fittings for their applications.
1. Tube Fittings
Tube fittings are essential components that connect two or more tubes. They come in various styles, such as straight, reducing, and angular, allowing for flexibility in design and function.
2. Ferrule Fittings
Ferrule fittings provide a secure grip on the tubing, preventing leaks and ensuring a tight seal. They are available in single and double designs, each suited for different levels of pressure and application requirements.
3. Forged Pipe Fittings
Forged pipe fittings are created through a forging process, resulting in stronger and more reliable fittings. They are often used in high-pressure and high-temperature applications.
4. Threaded Pipe Fittings
Threaded pipe fittings connect pipes using threaded ends. This type of fitting is often found in plumbing and other systems where disconnection and reconnection are necessary.
5. Flanges
Flanges are used to connect two pipes or pipe fittings together, forming a secure and leak-proof joint. They play a crucial role in the integrity of pipelines in various industries.
6. Check Valves
Check valves prevent backflow in systems, ensuring that fluid flows in only one direction. This is vital for maintaining system pressure and preventing contamination.
7. Ball Valves
Ball valves control fluid flow with a spherical disc. They are known for their durability and are often used in applications requiring quick shut-off capabilities.
8. Needle Valves
Needle valves allow for precise flow control, making them ideal for applications where accurate adjustments are necessary.
9. Manifold Valves
Manifold valves enable multiple connections, combining several functions into a single compact unit, effectively controlling and directing flow.
10. Double Ferrule Tube Fittings
Double ferrule tube fittings feature two ferrules that provide a double seal, enhancing safety and reliability in high-pressure applications.
11. Single Ferrule Tube Fittings
Single ferrule tube fittings are simpler in design but still offer a reliable connection for moderate pressure applications.
12. NPT Fittings
NPT fittings (National Pipe Tapered fittings) are designed to create a tight seal between two tapered male and female threads, often used in piping systems for gas and liquids.
Choosing the Right Manufacturer: Techtubes.in
When selecting instrumentation tube fittings for your project, choosing a reputable manufacturer like Techtubes.in is crucial. Here are some factors to consider:
- Quality Standards: Ensure that the manufacturer adheres to international quality standards such as ISO and ASTM.
- Material Options: Look for manufacturers that offer a variety of materials, including stainless steel, carbon steel, and alloy selections.
- Customization: The ability to customize fittings to meet specific project requirements is vital for many industries.
- Technical Support: A dependable manufacturer should provide technical support and guidance throughout the selection process.
Applications of Instrumentation Tube Fittings
The versatility of instrumentation tube fittings allows them to be used in various industries, including:
1. Oil and Gas Industry
Instrumentation fittings are essential in the oil and gas industry for transporting liquids and gases safely. They help maintain the integrity of pipelines and prevent leaks that could result in catastrophic failures.
2. Chemical Processing
In chemical processing, fittings are used to convey corrosive and high-temperature fluids. Choosing the right material for the fittings is critical to ensure compatibility with the chemicals being transported.
3. Pharmaceuticals
The pharmaceutical industry requires strict adherence to sanitary standards. Instrumentation tube fittings used in this sector must be easy to clean, resistant to corrosion, and able to withstand high pressures and temperatures.
4. Food and Beverage
In food and beverage processing, ensuring hygiene is paramount. Fittings must be made from food-safe materials and designed to minimize contamination risks.
5. Power Generation
Instrumentation fittings are integral to power generation systems, where they help control the flow of steam and fluids in turbines and other energy-producing equipment.
Conclusion: The Future of Instrumentation Tube Fittings
As industries continue to evolve, the demand for instrumentation tube fittings is expected to grow. Advancements in materials and manufacturing techniques will lead to even more reliable and efficient products. Choosing the right instrumentation tube fittings manufacturer is crucial for ensuring safety and performance in critical applications. By understanding the different types of fittings, their applications, and the importance of selecting a quality manufacturer, businesses can enhance their operations and maintain a competitive edge in their respective markets.
For more information on reliable instrumentation fittings, visit Techtubes.in. Harness the knowledge and expertise of a leading manufacturer to meet your industry needs.